Porady
Uwaga! Poniższy opis został przetłumaczony automatycznie.
Informacje na temat Siemens SIMATIC S7
Co to jest Siemens SIMATIC S7?
Jak zbudować kontroler PLC?
Kryteria zakupu dla kontrolera PLC
Co wyróżnia kontroler Siemens SIMATIC S7?
Jaki system S7 do jakich celów?
Co to jest Siemens SIMATIC S7?
Siemens SIMATIC S7 to kontroler PLC. Sterownik PLC oznacza sterowanie z możliwością zaprogramowania pamięci. W angielskojęzycznej części urządzenia te są znane jako sterowniki logiczne z programu (PLC). Sterownik PLC służy do sterowania i regulacji maszyny lub urządzenia, na przykład w przemyśle do sterowania przenośnymi taśmami. Kontroler jest zaprogramowany cyfrowo, aby móc obsługiwać maszynę z logiką oprogramowania. Sterowanie z programowalną pamięcią działa za pomocą oprogramowania, podczas gdy konwencjonalne, programowalne sterowanie (VPS) steruje urządzeniami końcowymi na stałe okablowanymi przez przekaźnik i styczniki. W przeciwieństwie do VPS, PLC jest bardzo dynamiczny i może być indywidualnie dostosowywany do danego scenariusza aplikacji bez konieczności zmiany go po stronie montażu. Sterownik PLC posiada zainstalowany na stałe system operacyjny i może załadować zapisane przez użytkownika programy przez interfejs pamięci.
Jak zbudować kontroler PLC?
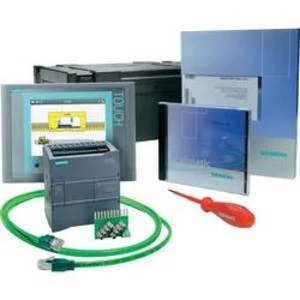
Kontroler PLC posiada z reguły wejścia dla czujników i wyjść do tak zwanych elementów wykonawczych. Na podstawie wartości wprowadzanych, które czujniki dostarczają do sterownika PLC, elementy wykonawcze są sterowane przez jednostkę CPU kontrolera PLC. Na przykład okna można otworzyć, gdy tylko osiągnięta zostanie określona temperatura, lub taśmy przenośnikowe można uruchomić, gdy obecny jest określony ciężar. Za pomocą analogowych przetworników cyfrowych (ADU) można przetwarzać nie tylko sygnały z czujników cyfrowych, ale także analogowych. Analogowe grupy wyjściowe mogą z kolei być sterowane przez przetworniki cyfrowo-analogowe (DAU).
Dzisiejszy kontroler PLC jest zasilany napięciem 24 V DC. Procesor jest centralną jednostką obliczeniową kontrolera PLC i obejmuje, oprócz procesora, niezbędne zakresy pamięci dla oprogramowania sprzętowego i przetwarzania danych.
Mimo że istnieje norma dla kontrolerów PLC, norma IEC 61131, większość systemów PLC nie jest ściśle przestrzegała, a zatem systemy różnych producentów z reguły nie są ze sobą kompatybilne.
Kontroler PLC posiada z reguły wejścia dla czujników i wyjść do tak zwanych elementów wykonawczych. Na podstawie wartości wprowadzanych, które czujniki dostarczają do sterownika PLC, elementy wykonawcze są sterowane przez jednostkę CPU kontrolera PLC. Na przykład okna można otworzyć, gdy tylko osiągnięta zostanie określona temperatura, lub taśmy przenośnikowe można uruchomić, gdy obecny jest określony ciężar. Za pomocą analogowych przetworników cyfrowych (ADU) można przetwarzać nie tylko sygnały z czujników cyfrowych, ale także analogowych. Analogowe grupy wyjściowe mogą z kolei być sterowane przez przetworniki cyfrowo-analogowe (DAU).
Dzisiejszy kontroler PLC jest zasilany napięciem 24 V DC. Procesor jest centralną jednostką obliczeniową kontrolera PLC i obejmuje, oprócz procesora, niezbędne zakresy pamięci dla oprogramowania sprzętowego i przetwarzania danych.
Mimo że istnieje norma dla kontrolerów PLC, norma IEC 61131, większość systemów PLC nie jest ściśle przestrzegała, a zatem systemy różnych producentów z reguły nie są ze sobą kompatybilne.
Kryteria zakupu dla kontrolera PLC
Ważne cechy przy zakupie kontrolera PLC to:
- Czas cyklu: Określa czas trwania cyklu, w tym wszystkie zadania komunikacyjne. Cykl składa się z procedur rozruchu procesora, wczytywania wszystkich wejść, a tym samym danych z podłączonych czujników, przetwarzania szeregowego instrukcji programowych, zapisu wyników programu do obszarów danych kontrolera oraz sterowania grupami wyjściowymi lub elementami wykonawczymi. Z reguły procesor przerywa cykl, gdy trwa zbyt długo, co może mieć miejsce na przykład wtedy, gdy wykonywany program jest źle zapisany.
- Czas reakcji: Czas reakcji oznacza czas między zmianą sygnału wejściowego a reakcją ze względu na zmianę sygnału wyjściowego. Wskazuje również, jak szybko elementy wykonawcze podłączone do wyjść kontrolera PLC mogą reagować na nowo zmierzone wartości czujników.
- Rozmiar obszaru flagi: Obszar flagi służy do przechowywania wyników pośrednich. Flaga zawiera dane w formatach bit, bajt, WORD lub DWORD. Im większy obszar, tym więcej danych można tam zapisać. Wpływa to na szybkość obróbki cyklu i powoduje krótszy czas cyklu w przypadku większości programów.
- Obsługa HMI: HMI jest w tym kontekście interfejsem Human Machine i jest obecnie często realizowana w formie ekranu dotykowego. System SIMATIC S7 oferuje zaawansowany system z różnymi panelami z panoramicznym wyświetlaczem o rozmiarach 4, 7, 9 i 12 cali. Systemy HMI można obsługiwać zarówno za pomocą przycisków, jak i poprzez dotykowe wprowadzanie danych. Ponadto za pomocą złącza USB można podłączyć mysz, klawiaturę oraz skaner kodów kreskowych i przesyłać dane na pendrive USB.
- Skalowalność systemu PLC: Siemens oferuje skalowalny system z licznymi modułami rozszerzającymi i sterującymi, który można zamontować na szynie kapeluszowej bez większego wysiłku.
- Dopuszczenia systemu SPS: Coraz ważniejsza staje się zgodność z normami krajowymi i międzynarodowymi systemu SPS. Należą do nich normy cULus, FM, ATEX, CE oraz EN 61000-6-4, 60068-2-X i 61131-2
Co wyróżnia kontroler Siemens SIMATIC S7?
Oprogramowanie i części zamienne
Siemens SIMATIC S7 to najbardziej znany i rozpowszechniony PLC. W starszej serii S7-200 kontroler jest dostarczany z oprogramowaniem Step7Microwin, w serii S7-300 i S7-400 z obecnie popularnymi oprogramowaniem Step7. Następca 2020 jeszcze dostępnej serii S7-300 w serii S7-1500 jest już gotowy. Dla S7-300 w ciągu 10 lat od zatrzymania produkcji nastąpi zabezpieczenie części zamiennych.
Specyfikacja:
Od serii S7-400 grupy sygnałów można podłączyć pod napięciem i podłączyć (Hot-swapping). Dzięki temu podczas eksploatacji możliwe jest rozszerzenie urządzeń i operacje transferu podzespołów.
System S7 Siemens charakteryzuje się bardzo wysoką wydajnością do urządzeń peryferyjnych i/o, między innymi dlatego, że moc procesora od serii S/7-400 może być skalowana dynamicznie. W tym celu można obsługiwać kilka procesorów CPU w jednym urządzeniu centralnym. Możliwe jest przypisanie poszczególnych złożonych zadań, takich jak sterowanie, przetwarzanie lub komunikacja do poszczególnych procesorów w dedykowany sposób, optymalizując w ten sposób czas procesora. Prowadzi to do lepszej wydajności przy dużym obciążeniu.
Ponadto dzięki narzędziom SIMATIC Engineering jest możliwe efektywne projektowanie i diagnozowanie pracy w programowaniu. Oferują one różne języki, jak np. SCL oraz narzędzia graficzne do sterowania sekwencją, wykresów stanu i planów technologicznych.
Dzięki własnemu MPI (interfejsowi wielopunktowemu) firmy Siemens możliwe jest także pokonywanie dużych odległości w transmisji danych. W tym celu pomiędzy dwoma uczestnikami MPI można przełączać maksymalnie dziewięć repeaterów.
Programowanie
W przeciwieństwie do normy IEC 61131, w przypadku Siemens SIMATIC S7 jako programisty musi być adresowany samodzielnie dane globalne. Do tego celu dostępne są różne zakresy zapisu. Ponadto sygnały wejściowe i wyjściowe nie są włączane poprzez deklarowanie zmiennych na adresy, lecz przez odniesienie do wartości w schematach postępowania PAE i PPA z operandami E i a oraz ich adresami. W przeciwieństwie do systemów PLC, które są zgodne z normą IEC 61131, deklaracje zmiennych w Step7 odgrywają zatem niewielką rolę.
Jaki system S7 do jakich celów?
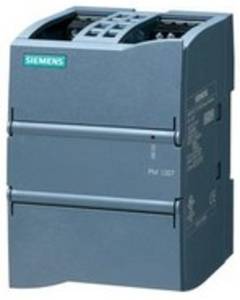
- S7-300: Do małych systemów sterowania w dolnym i średnim zakresie mocy. Obejmuje to na przykład maszyny tekstylne, maszyny pakujące, ogólne maszyny i urządzenia sterujące, maszyny do narzędzi, techniki instalacyjne oraz zastosowania w przemyśle elektrycznym i w elektryce.
- S7-400: Do średniego i górnego zakresu mocy. Seria S7-400 charakteryzuje się możliwością redundancji urządzeń peryferyjnych i/o. Dzięki temu można tolerować np. awarię procesora, magistrali PROFIBUS lub zespołu sygnału.
- S7-1500: Ta seria ma zintegrowane funkcje bezpieczeństwa i ochrony. Obejmuje to na przykład ochronę know-how w oparciu o hasło przed nieuprawnionym odczytaniem i zmianą elementów programu oraz ochronę przed kopiowaniem przed ich bezprawnym powielaniem. Ponadto seria ta po raz pierwszy zawiera koncepcję uprawnień ze stopniami uprawnień oraz ochronę przed manipulacją danymi inżynieryjnymi. Połączenia Ethernet mogą być zabezpieczone poprzez zintegrowany Firewall i połączenie VPN. Poza tym w tej serii analiza systemu jest już zintegrowana z procesorem CPU. Dzięki temu informacje systemowe są udostępniane bezpośrednio przez jednostkę centralną, a następnie mogą być odczytywane w portalu HMI, portalu TIA, a także przez wyświetlacz lub za pośrednictwem wbudowanego serwera WWW.